By David Archer
Copyright David Archer 2010
Note: I sculled for twenty years in California, Wyoming and Montana. After a ten year hiatus and two total shoulder replacements, I will give it another try this fall in my own scull boat design, which is similar to the Humboldt design.
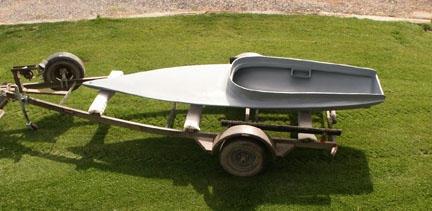
Hunting ducks on open water in a scull boat had its beginnings during the market hunting era on both the East Coast and the West Coast. With the improvement in boat construction using fiberglass materials, sculling saw a resurgence during the 1960's and 1970's. Today dedicated scullers still ply their stealthy craft on waterways across the country. It is a small fraternity of men, however, and sometimes it can be tough to find a mentor. Much information may be gleaned from an on-line sculler's forum and other dedicated sites. The following article covers the basics before someone attempts to buy a boat and learn on his own.
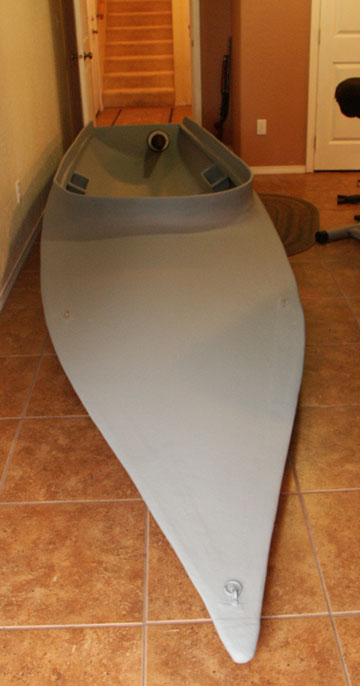
A traditional West Coast two-man scull boat is 14' in length and powered by a long, slender sculling oar that exits the stern through a rubber boot. Laying on his back, the sculler adjusts the oar so that the curved part of the blade is facing up and the flat side facing down. If you are right handed, the starting position would be to grip the end of the sculling oar so that your clenched hand is holding the oar in a straight line, resting slightly over your left shoulder. The sculling motion is a figure-eight rotation of your wrist. This pushing and pulling motion propels the boat forward. However, if it is not a fluid motion, the boat will rock from side to side. Do not exaggerate the figure eight motion. Keep it tight. If I am at rest and want to begin the process, I would cock my wrist in the downward motion, which then tips the blade on its side. I would then pull the handle up towards the top of the figure eight. At that top point I would rotate or cock my wrist back so that my next motion would be a push motion. The pushing motion would drop slightly to the bottom of the figure eight. At the top of the stroke, I rotate my wrist to the downward stroke and pull back. Naturally, the wider the figure eight and the slower the movement and the boat will begin rocking or moving more to one side or the other.
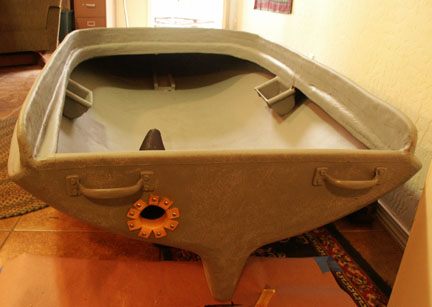
Turning the boat slightly necessitates that you either pull or push the oar in the figure-eight motion. For example, if the sculling oar is in the correct position with the flat bottom facing down, and you rotate your wrist and pull or push the oar, the nose of the boat will glide around to the new position. However, after each push or pull, you will need to re-position the oar straight behind you, flat side down so that it can slice through the water and not block the boat's turning progress. You wait to make some progress before repeating a push or pull movement. Slight adjustments while sculling is just a mater of prolonging a push or pull action slightly longer. (Yes, it is possible to scull in reverse, but I could never get my mind wrapped around the mechanics so I was never successful.)
Since the sculling boat has a long keel on the bottom, the keel helps track the boat in a straight line. Nonetheless, the trick is to keep the figure-eight strokes short so that before the boat goes off its straight line, the sculler adjusts or shortens the stroke with the opposite push or pull stroke. To increase speed, the left arm is lifted up so it is resting on top of the sculling oar with the left hand gripping the oar just in front of the right hand. You generally have to scrunch your body and shift to the side a bit, but this two-handed approach allows us weaklings a strong method for "sprinting" or closing the distance just before you sit up to shoot. Strong men close while sculling with their left arm and hold their shotgun with the right hand so that they lose no time sitting up and getting off a shot.
Most scullers use a kayak paddle or a set of oars when they want to retreat from rough water. In the past, I kept my life jacket as a pillow to prop up my head. The idea is that you want to have your eyes barely peaking over the front combing. (Black face) Because of the possibility of a wave rolling up the deck, a small combing is essential. Years ago the Lynn-Lee scullboat was equipped with a canvas wind shield. Similar to an old baby buggy, the windshield (wave shield) would pop up and be secured with two bungee cords.
The boat would seem dangerous, but I have been out in choppy water in three separate designs, and I always felt safe with a few exceptions where I found myself a mile from shore in rough water. In this situation, pull out the stowed outboard motor and head for shore using your kayak paddle to negotiate the waves. Another safety measure is too toss your lead weight overboard. Since you need about a 70 pound, lead ingot shoved to the very tip or bow of the boat, the easiest method is to have a long rope attached to the ingot. (This bow weight is to keep the bow tip as close to the water as possible. Birds looking at the approaching scull boat see a deck that gradually rises from the water to the combing. It looks like a partly submerged floating object.) At the end of the rope, attach the floating rope to a decoy. If the water is not too deep, the decoy will mark the spot so that you can retrieve the weight later. In twenty something years of sculling, I had to do this only once, although a number of times I pulled the weight to the center of the boat to keep the nose pointing up during rough weather.
So, just what is safe? I have seen scullers in really rough, choppy water, but I thought they were foolish. I head for shore when the gentle waves start lapping my boat or when I find that the boat is hard to control when it is lifted up in front. During rough weather, work the shoreline in two to three feet of water. It is hard to get off a good shot due to the rocking motion of the boat, but you will be amazed at how close you will get to the birds that have landed and walked up to the shore. I have also worked geese close to shore with two to three feet of waves. I would get within ten yards, but when I would drop into a trough, they would disappear. And when I tried to get off a shot, a wave would push me out of alignment. It was pretty funny the times that I would try it from the safety of near shorelines.
Scull boats make excellent layout boats in the marsh or in flooded fields. As always how well you cover the boat is a key factor. Remember also that you have a limited shooting arc of shoulder movement. You do not need camo or netting when you are sculling out in open water. The preferred color is dull, battleship gray.
Open water sculling is exciting. It is the essence of sneaking up on resting birds out in the open water. It can also be frustrating because larger flocks tend to jump early sending the entire raft into the air before you are in range. Ah, shit! You say to yourself as you sit up to stretch. To your great surprise a few singles in easy range jump when you sit up to stretch. Always sit still and survey the area before you sit up to stretch. I can't tell you how many single geese I have taken after the roar of thunder when a big flock got nervous and took flight. Early on in my learning curve I thought the remaining singles or pairs were wounded or crippled birds, but when I pursued them too fast, they would jump up and fly away! (You will need a good set of binoculars to spot birds that are worthy of a 100-yard scull.)
If you are new to the sport, pick off the trailing pairs and try and gradually separate them from the big flock. I would say that if you take your time, don't rock the boat or show too much of the boat's side profile, you have a good chance to separate birds and get off a shot. Regarding the first shot, I will say up front, that I have peppered resting birds with a sluice shot on open water many times. Giving how much work it is to spot a raft, sneak up on them and close the range, I will not apologize for occasionally sluicing birds on open water. Most of the time it is not necessary. Many times you will sit up and they freeze in shock. I have missed easy shots when this happens.
One effective open water tactic is to set a dozen decoys out in open water. Back off a hundred yards and drop a lone goose decoy or magnum mallard with a heavy weight. Tie your scull boat to the anchored decoy and stay put until birds land in the decoy zone. Sometimes after a scull you will head back to your anchor decoy and suddenly see two or three birds hanging out at your previous resting spot. Use the sun so that it is behind you. Resting birds don't like to look into the sun for very long if they think that you are just a slow drifting log or object. Fog is good until you get lost and birds appear out of nowhere ten feet from the boat. Needless to say too much fog defeats the purpose. I never wanted hamburger in the bottom of my boat.
Sculling into bays can be very effective. I have sculled on birds until I hit the mud and stopped forward progress. I have been within fifteen yards. Pick a single bird and stay with it until it drops. These are weird situations, and when I was young I would have visions of birds falling out of the sky with three shots! Flock shooting is a difficult lesson to learn. I ounce worked my sculling boat on swimming geese that headed to a flock of geese just off the shore. They went right into the "dekes". When I realized what I had done, I sat up unarmed and the birds took off right in their spread. Two Montana hunters stood up without shooting. They had a safe shot, but they too were shocked with the entire episode. They had never seen a scull boat before, and when they realized what I was doing they decided to honor my scull. Too bad no one shot as all three of us could have had a safe shot. They told me that if I could do it again at a safe angle, we should all shoot. I just laughed but later in the day I chased some mallards towards their spread. The birds got nervous and jumped up and flew into their decoys. Safely out of distance I watched them drop some mallards. I would think that a sculler at one end of a small lake would really be able to keep the birds moving down lake to a waiting layout boat hunter.
If you can get on a lake safely during winter, hunting the ice edges can be awesome. Bring a fishing pole with a nasty lure with large treble hooks to retrieve downed birds on the ice. Never go on the ice! Never go on a lake during winter unless you have an easy put-in and take-out! Don't bring a dog with you! Only go out on blue-bird days. Throw a white sheet on the deck, wear a white hat and jacket and you will have a blast. Finally, if you have a wet suit, wear it. To often, however, young men tend to push the envelope of safety resulting in tragedy. Regarding winter conditions, never scull on rivers! Scull boats cannot be turned sharply or quickly maneuvered. The only type of river I would scull on would be very slow stretches such as can be found on the Jefferson. Scull boats are not designed for rivers!
You will find many sculling sites on the Internet. You can still buy a boat in the Humboldt Bay area (Eureka, California). I do not believe that flat bottom sculling boats made out of wood are as effective as traditional designs. If I ever get around to posting this on my blog site, I'll post some of my old photographs, along with the scull boat that I am presently building. Heavier scull boats track in a straight line better than light boats. This is a fact. My best boat was a HEAVY wood / fiberglass boat. It had a FULL running keel. The cockpit combing was so high compared to other scull boats that it had a notch cut out up front to track the birds. I bought it from a man in Eureka who wanted to buy a two-man scull boat. That boat was the best damn boat I ever owned, and I have owned five scull boats, and I am presently building my last boat. One stroke and it would glide in a straight line effortlessly. I sold the boat to a friend so that I could have a two- man boat. Later the man who sold it to me tried to track the boat down after my friend sold it! Even when I was young, I would struggle loading it into my truck. I should have...yeah, I sold my 39 Chevy when I got out of the Army too!
Finally, the first season of sculling is quiet often disappointing. During the 70's I would watch men try and scull and end up selling their boats before the season was over. I didn't get many birds my first year, but I started getting close limits the following year. It is important that you have someone give you a lesson on sculling. Sit up on the deck combing and video-tape the lesson. Get on the sculling forum and ask questions. If you are going to hunt on open water far from shore, have someone on shore to come out for you in a "mother" boat if the weather changes. Cell phones are great for that situation. Better yet, tow the scull boat on a scouting trip and take turns with a friend during the middle of the day!
General Observations:
Closing the distance: Remember that when you are sculling or chasing birds on open water, they are swimming away from you. When they jump, you are shooting not their exposed breast and belly but their backs. You must be close for a clean kill, and truth be known, you end up shooting a lot of cripples on the water. Also keep in mind that when the birds jump, they are going to get a couple of wing beats, five to ten yards, before you can sit up, take aim and fire. (Shoot slightly under the birds as they rise off the water flying away from you.)
Study their behavior: If they stall and shift around, they are ready to jump. If you can see color and details, they are in range. If you have a pair that keeps turning left and then right to look at you while they are swimming, wait until they turn to a profile and then take the shot. Geese will simply try and out swim you so use two hands to close the distance or back off and go slower. If a couple of ducks or an entire raft jump when you are just out of range, NEVER fire. If you stay down, they will most often just glide a hundred yards and then land. I have closed in on geese like this two to three times before I dropped one or more of them. Again, remember that there will always be a few birds close by that stay on the water.
Blacken your face and keep your hands down: If geese swim to shore before you close the distance, they have an advantage as they can stretch their necks up and look inside your boat. If they see your arm or wrist move, they will sound the alarm. (90% of the birds that you flare will be because they saw your wrist move above the combing. Use a black golfer's glove to protect against blisters and camo the rest of your hand, along with your ENTIRE face, and NEVER move your head around to see which birds you will scull towards.) Just as you will have frustrating days wondering what you did wrong, you will have easy days when you scull within ten yards of ducks or geese.
Calm, sunny days are best because the boat has no chop slapping against the boat, and your scull can be smooth, silent and deadly.
Practice before the Season: It is essential that you practice your sculling techniques during the summer, and while you are at it, troll a fly or lure. The silent flash of the sculling oar attracts fish! The greatest challenge is to drop the oar and set the hook. The easiest birds to scull on are mallards, pintails and Canada geese. The most difficult birds to scull on (from my experience) is widgeon. They are nervous birds in a flock. They will start a roll where the nearest group flies up to the front positions, and then the roll continues.
Only use your binoculars for spotting and targeting birds. Sometimes you will lose them in the glare or fog and you will have to glass again to ascertain your bearings. Over-and-over again, throughout my years, I would spook birds that were close by when I slowly lifted up the binoculars. Sometimes it would be reflection off the lens, and sometimes it would be the movement.
Always blacken your face. If you wear glasses, use a single lens, as when you are laying on your back the bi-focals will get in your way.
If you penetrate a flock and parted birds see your side profile and movement of the oar out through the transom, they will flare. The biggest problem with sculling is heading into shore and running out of water. It sure is frustrating coming to a halt with undisturbed sleeping birds just out of effective killing range. If you scull shallow water, you will need a sculling blade that is straight versus the slightly dropped blade, which is most common. You need both types of blades on hand for shallow conditions.
Blades are made in a variety of materials and fiber glassed to a wood 1 ¼" closet pole. Here is what I have.
Blade length: 36 inches (rounded on top the height of the blade tapers to the tip of the blade. The blade and the handle are encased in cloth and resin)
Blade width: 3.5+ inches
The blade tapers to the tip at ¼ inch.
Where the blade connects to the pole, the thickness is 1 ¼ inch where the top of the blade slips into a vee in the pole. These measurements are the finished product when it is glassed. The notched vee in the pole and blade is 7 to 8 inches. Use a resin grout to fill any cracks, and then sand and shape it smooth and use cloth and resin from the tip up the pole for about eight inches. Sand and paint gray. (Tip: Cut a small V where your hand grip goes. This will indicate the correct position of the blade indicating correctly that the rounded or contoured edge of the blade is facing up. This is always the starting position.
I once had a shorter and fatter blade. The blade was made in a plaster mold with a balsa wood core. It too was a good blade. The key is that the blade must be flexible, even whippy.
I hope this helped.
Dave Archer
541-783-3796